INTRODUCTION
What is soldering and how is it used?
Soldering is a fabrication technique that joins two or more metallic components together by melting a filler material called solder. Once cool, the solder creates a durable joint.
Soldering is utilized in many research and technical spaces on campus, such as maker spaces, laboratories, and research centers. Different soldering applications range from electronics research to art and metal work. On our campus, electric based soldering is the most common type of soldering. This process involves heating the components to be joined and the solder using a tool called an iron. Other techniques that use open flame or propane will require special considerations and permitting.
Solder and flux
- Lead Alloy Solders- Known as soft solders, lead is mixed with other alloys to achieve the required melting point and tensile strength. The most common alloy along with the lead in this mixture is tin. Because of lead’s toxic nature, use of lead-free alternatives are encouraged whenever possible.
- Lead-Free Solder- Solder that does not contain lead in the alloy mix. These solders tend to have a higher melting point than lead based solders. Alloys can include metals such as tin, copper, zinc, silver, arsenic, cadmium, beryllium, and nickel.
- Flux and Flux-Core- Flux is a reducing agent made from rosin or acid and is used to remove the oxidative layer that forms on the metal, effectively cleaning the metal. This helps to improve the bond between the soldered components. It also improves solder’s effectiveness and overall flow. Flux can either be incorporated into the solder (flux-core) or be applied separately as a paste or liquid.
Solder Core Styles
- Solid Core- Consist of a solid wire comprised of the solder alloy or material. Flux must be applied separately in the cases where solid core solder is used.
- Acid Core- Solder that is formed into a wire with a hollow core that is filled with an acid-based flux. This is a stronger, more aggressive form of cleaning flux. These solders are intended to be used for steel or other metals and requires the flux residue be neutralized or removed after the soldering operation is completed to avoid corrosion of the soldered components.
- Rosin Core- Solder that is formed into a wire with a hollow core that is filled with a milder variety of flux made of rosin, derived from pine trees. The flux residue associated with rosin core solder is non-corrosive and therefore does not need to be removed or neutralized after soldering. Making it desirable for electrical applications where it may be difficult to remove the flux residue. This type of solder is cost effective and easy to use. Even though rosin flux is easier to use, it is still an occupational hazard and must be used with caution.
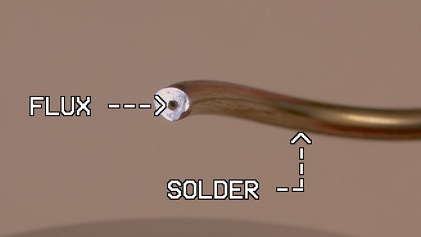
Source: Wikimedia: Kevin Hadley
OVERVIEW AND MITIGATION OF HAZARDS
Identifying, understanding, and assessing hazards allows us to acknowledge the risks they pose. Accidents are inevitable, but with careful planning they can be significantly reduced. Know which risks can be eliminated with removal or substitution and what risks can be reduced with safety measures.
Thermal
Electric soldering iron temperatures can range from 300°F to 900°F, depending on the application. Serious burns and ignition of flammable materials can occur at these temperatures. Users can also be exposed to serious burns if the materials spatter. This happens when materials erupt causing an explosive spray of hot flux and/or solder.
- Avoid direct contact with soldering iron tip, flame from torch, or the materials being heated. Use clamps or tweezers to hold wires and other materials. Heat resistant gloves can also be worn to prevent burns.
- Do not rest the iron on any surface other than the stand that was provided by the manufacturer.
- Turn off and/or unplug soldering irons when not in use. This includes stepping away from the workspace. Although some irons may come equipped with safety timers, it is best practice to not rely on this function and manually switch off the unit.
- When using a traditional sponge to clean the tip of the soldering iron, ensure it is always wet and does not dry out.
- Do not solder in areas where flammable materials are kept.
- Give the soldering surface and its components time to cool before touching it to prevent burns.
Chemical Exposure
The chemicals and metals used in these processes can pose risk to a user through direct contact or by exposure to fumes and vapors. Solder can contain heavy metals including but not limited to; lead, tin, copper, nickel, selenium, arsenic, cadmium, beryllium, and/or silver. Exposure to these chemicals can cause immediate health effects or can build over time and create short- or long-lasting health problems. Both rosin and acid core solder can cause skin and respiratory sensitization or irritation. Each subsequent exposure can then cause a worsening response. Exposure is most likely to occur through the inhalation of fumes and ingestion.
Consideration must also be given to the surfaces where the soldering will happen. Fumes can be generated from the decomposition of coatings, paints, or residues. The solvents used to prep surfaces can also give off toxic fumes or vapors.
- Clean surfaces well before soldering. This will prevent volatilization of any residues, solvents, or coatings.
- Use lead-free solder whenever possible.
- Frequent hand washing can prevent chemical exposure by ingestion. The use of gloves is also recommended if you are handling solders. Hands should be washed when soldering is complete, before exiting the soldering area, before eating and drinking, and before leaving for the day. Remember to wash your hands each time your gloves are removed.
- Limit time spent soldering by completing projects as they surface rather than waiting for projects to accumulate. Exposure is reduced when soldering is conducted for only 15 minutes versus one hour.
- Use proper ventilation. The fumes and smoke generated from soldering can cause respiratory and eye irritation.
- Ventilation standards are different in labs versus regular offices. Bench top fume extractors with carbon and/or HEPA filters are sufficient for most applications. Alternatively, building controls like fume hoods and snorkels can be used if they are available and are in working order.
- Read and become familiar with the safety data sheets (SDS) so you are aware of the hazards associated with the materials being used.
- Clean contaminated surfaces and work areas once work is complete to avoid accidental exposures. Use soap and water to clean surfaces or materials designed to clean metal contamination (e.g. D-Wipes).
- Elevate the working surface to keep the fumes directed away from your face. This will help to improve posture and prevents your face from being in the fumes being generated. If elevation is not possible keep your head to the side and not directly above what you are soldering.
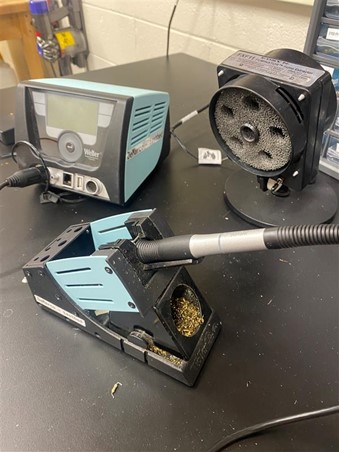
Source: MRL Laboratory
Electrical
Electrical shocks can happen from exposed wiring, wiring that is not properly grounded, and soldering on equipment that is energized.
- Never solder anything that is energized.
- Soldering irons can easily melt through insulation on power cords causing electrical shocks and burns.
- Always inspect equipment before use. Old equipment with frayed cords or damaged insulation presents additional electrical hazards.
- Only use grounded (three-prong) outlets with three-pronged cords.
ADMINISTRATIVE CONTROLS
Administrative controls are used to improve safety by putting in place policies and rules that control the way that work is performed, such as SOPs, training, and reinforcing good work practices in the research space. Emergency protocols will help users to be familiar with what to do in an emergency.
Standard Operating Procedures
Developing SOPs for your specific operations will standardize procedures, work practices, and effectively communicate associated hazards. These are also valuable training tools. For more information on creating SOPs click here.
Things to include in your SOP documents should be; safety information such as hazards associated with the materials/chemicals (shock hazards, corrosive), how to set up the soldering area, step-by-step instructions on the operation of the soldering iron, required PPE, how long can be spent soldering, clean-up and waste disposal, and emergency procedures. Instructions provided by the manufacturer and the contents of this document often cover the necessary elements of a soldering SOP.
Training
Effective training supplies users with the knowledge and confidence to not only carry out the task, but also prepares the user for emergency situations.
- A senior researcher with experience in soldering should teach those who are unfamiliar with the technique.
- Training should cover both the SOPs and what to do in emergency situations.
Good Work Practices
Following these guidelines will not only produce superior results in your research but will keep users safe.
- Keep work area clean and organized.
- Use appropriate solder and flux for the scope of work being done.
- Practice good hygiene by washing hands thoroughly with soap and water when soldering is complete.
- Clean potentially contaminated work surfaces with soap and water.
- Never eat, drink, or apply cosmetics in areas where soldering will occur.
PPE
Wearing appropriate clothing and PPE will also minimize exposure and risk of injury.
- Gloves- Heat resistant gloves protect hands from hot materials. Chemical resistant gloves (such as nitrile) protects hands from chemical exposure and skin irritants.
- Eye protection - Solder can spit, bubble, and emit irritating fumes. Hot metal and cutting wires can also pose risks to the eyes. It is important to wear ANSI Z87.1-2010 certified eye protection. Safety glasses provide the minimum amount of protection from splashes and debris. Unvented safety goggles will provide a higher level of protection from fumes, splashes, and give impact resistance.
- Flame-retardant/resistant clothing- Cotton material is preferable to synthetic materials, as they are less likely to burn or melt when exposed to hot solder.
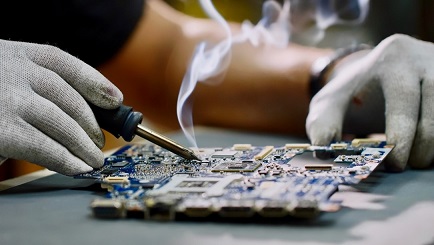
Source: AdobeStock
EMERGENCY RESPONSE
First Aid
Contact DRS immediately and submit an Event Report in the case of any incident or near miss. Also report these events to your supervisor or Principal Investigator. Please include where the incident occurred, the type of incident, and if there was an injury or property damage. For more information on emergency response click here.
Thermal Injuries
- Skin- If burned, run cold water over the burned area for 15 minutes. Do not apply any creams or ointments. Seek medical attention as needed.
- Eyes- Flush the eyes using emergency flushing equipment for at least 10 minutes. Seek medical attention immediately.
Chemical Exposures
- Inhalation- Immediately move to fresh air. Seek medical attention as needed.
- Skin/eye contact- Flush the area with water continuously for 15 minutes. Seek medical attention as needed.
- Ingestion- Do not induce vomiting, seek medical attention immediately.
Fire Response
Because of the heat generated from soldering irons, nearby flammable materials could catch fire. Electrical shock also poses a fire risk. Know where fire extinguishers are kept and how to properly use an extinguisher. If necessary, call 911.
HAZARDOUS WASTE
While soldering may not generate much waste, certain wastes must be collected and submitted to DRS for pickup.
Items that should be submitted for waste pickup include, but are not limited to:
- Solder and flux that is old, unused, and/or no longer needed.
- All lead Solder, solid-core and flux-core.
- All lead contaminated debris such as wipes, sponges, and components.